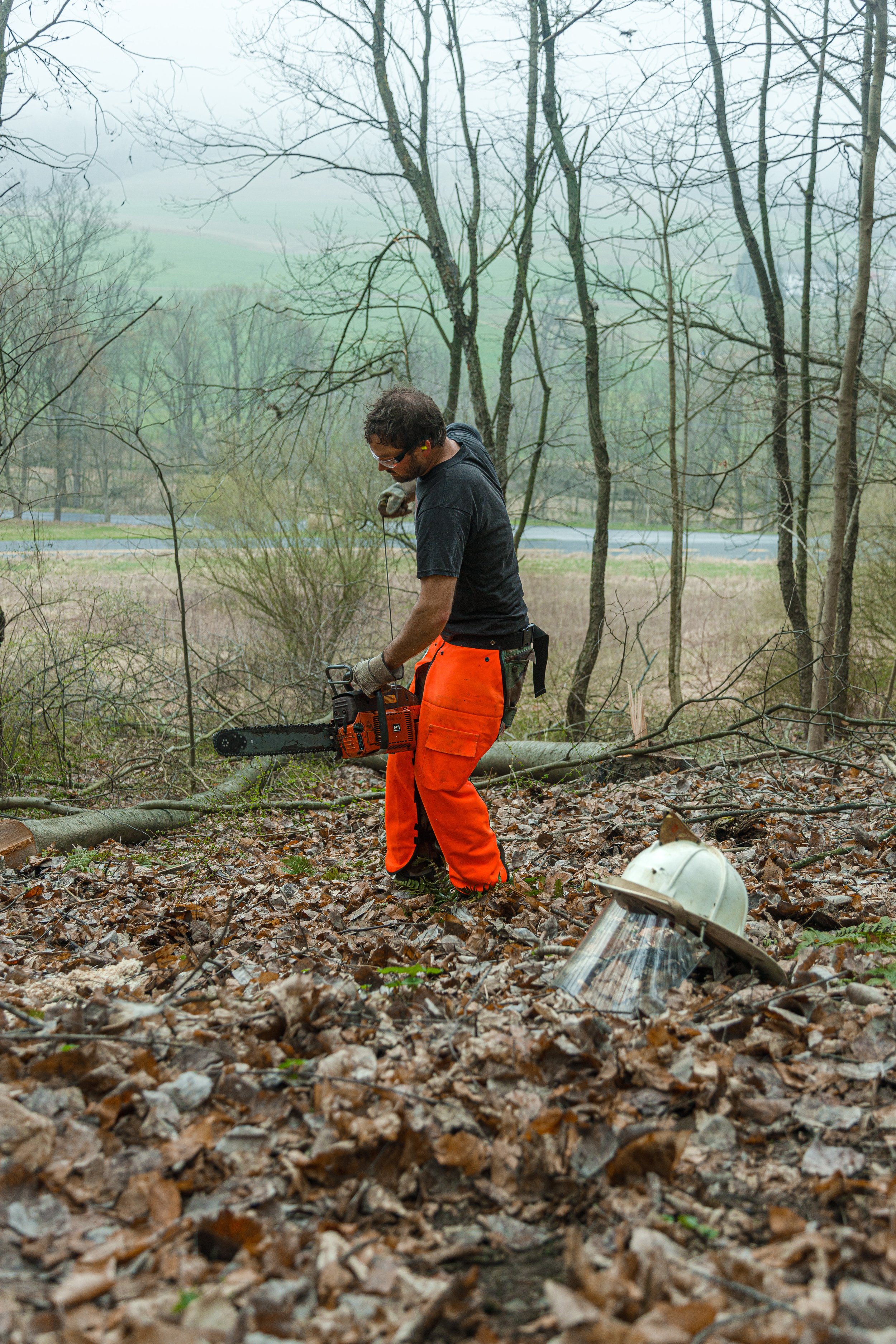
Woodworking is all about the material for me. Each piece of wood is a unique expression of nature and the will of the tree. I aim celebrate the singular nature of these pieces by responding to what I’m presented with and enhancing nature’s creation with my actions.
The ability to transform the material from tree to final product is a delight. For many years the most immediate way to make work from the raw tree to a useful and beautiful item was through what is called “green woodworking” which utilizes material that is freshly harvested and has a high mositure content. This material I source mostly from trees that fall in storms, that I remove for friend’s when the tree becomes a nuisance or hazard or even bits collected from the side of the road. These pieces are best suited to wood carving as the material is softer and more maleable than dried wood or bowls which can be turned thin and evenly then allowed to dry and warp without fear of cracking.
It’s long been my goal to make all my work from wood that I’ve obtained myself. This became a reality in 2021 when I purchased a bandsaw sawmill with 2 friends. With it, we’re able to cut boards and slabs for furniture and my signature cutting boards. The wood we use is stuff that’s fallen in storms on local farms or that we’ve removed and repurposed as one partner is a professional arborist.
Knowing where the wood came from and how it was obtained ensures that the material was harvested sustainably. Most of it would otherwise have been converted to firewood or left to rot. The wood is local, cutting down on the environmental impact and cost of transport. Further, we can be certain the woods and landscape haven’t been damage by heavy equipment and indiscriminate cutting.
Here you can see the rotten trunk of this birch tree, charcteristic of many of the trees on this hill. Many blow over as the rot progresses and the wood is useless. You can see my home shop below on the left.
Once the logs are gathered they’re loaded on the mill. Here I’ve cut all 4 sides off to create boards with parallel edges. Often, we don’t bother and leave the edges “live” with the bark and shape of the tree in tact.
These slabs will dry for a year or more in the barn at which time they’re dry enough to use for furniture.
This birch tree, just 200 yards from the shop, was dying so I cut it down along with a few other diseased trees. Being straight and large in diameter it will make good boards while the tops and some crooked sections will be saved for bowls.
Odd bits of wood, like this curvy stump are cut up with the chainsaw to make bowls. Here I’m laying out my cuts to get the largest bowl and a number of smaller ones.
The beech I’m turning here fell in a friend’s yard in nearby Kutztown. The pieces were extremely dense and heavy, so I cut them down for bowls.
The final little bits that couldn’t be made in to boards, slabs or bowls are cut on a band saw in to spoon “blanks” ready for hand carving. When I’m processing a lot of wood and have a large number of blanks I bad them up and freeze them to retain their moisture.
A tractor is a huge help dragging logs out of the woods and placing them on the mill. Fortunately, Matt is just 2 miles away and full of enthusiasm!
This walnut log was pulled out of the nearby creek. We’re cutting it into slabs for furniture.
This live edge desk was made from the above walnut slabs. It’s sealed with a durable epoxy finish to keep the bark secure and protect the wood.
The chainsaw is used to split this cherry log that we saved from a tree removal job. The areas to right and left of center will be bowls. The bit above the center or “pith” of the tree, which is unstable and rotten in this case, will be used for spoons.
I finish a lot of bowls with a bit of hand carving. This piece is being carved before a coat of food safe milk paint is applied.